Die Lebensmittelindustrie
Die Lebensmittelindustrie hat spezifische Anforderungen, die sowohl mit der Auswahl der Materialien als auch mit der Herstellmethode der Bauteile erfüllt werden.
Materialien
Die in der Lebensmittelindustrie verwendeten Materialien müssen sicherstellen, dass keine Moleküle aus dem Material in das Lebensmittel migrieren. Aus technischer Sicht ist rostfreier Stahl das beste Material für solche Anwendungen. Die Stahlsorte AISI 318 ist äußerst beständig gegen Säuren und Basen. Zahlreiche Produkte werden daher mit diesem Material hergestellt. Eine weitere in dieser Industrie verbreitete Edelstahlsorte ist die AISI 316. Beim Tiefziehen ist es natürlich besonders wichtig, die speziell dafür entwickelten Varianten zu verwenden.
Das italienische Dekret Nr. 72 vom 9. Mai 2019 schreibt vor, welche rostfreie Stähle für den Kontakt mit Lebensmitteln in Italien erlaubt sind. https://www.gazzettaufficiale.it/eli/id/2019/08/01/19G00079/sg
Aluminium ist ebenso weit verbreitet. Bei Aluminium gibt es Einschränkungen bezüglich des Materials, das mit Aluminium in Berührung kommt, und der Temperaturen, bei denen das Lebensmittel mit dem Material in Kontakt kommen kann. Die Anwendungen sind vielfältig. Bei direktem Kontakt von den Lebensmitteln mit dem Material wird normalerweise Stahl eingesetzt. Stahl ermöglicht auch den Einsatz von besonders aggressiven chemischen Putzmittel für die Reinigung und Desinfektion/Sterilisation der Komponenten. Aluminium wird dagegen verwendet, um das Gewicht der Komponente zu reduzieren oder wenn ein optimaler Wärmeaustausch zwischen der Komponente und den Lebensmitteln erforderlich ist (aufgrund der Wärmeleitfähigkeit von etwa 200 W/mK von reinem Aluminium 1050 gegenüber 15 W/mK von Stahl AISI 318).
Die Firma F.lli Poli hat Ihre Produktionskapazität schrittweise an die Verarbeitung unterschiedlicher Materialien angepasst. Behälter für Lebensmittel oder Getränke, Gestelle von Maschinen, die mit Lebensmitteln in Berührung kommen (Geschirrspüler, Backöfen und dergleichen) und auch Maschinen für die Verpackung/Sterilisation von Lebensmitteln werden normalerweise aus rostfreiem Stahl hergestellt.
Das liegt auch daran, dass dieses Material die Reinigung mit sehr aggressiven Putzmitteln ohne Schaden an der Oberfläche ermöglicht. Schalen für die Kaltbewahrung von Lebensmitteln werden dagegen aus Aluminium hergestellt, denn Aluminium beibehält seine mechanischen Eigenschaften auch bei sehr niedrigen Temperaturen.
I generellen Anforderungen, denen alle Lebensmittelkontaktmaterialien entsprechen müssen, sind durch die Rahmenverordnung EG 1935/2004 geregelt.
Die LKM Vorschrift
Die Produkte, die in der Lebensmittelindustrie verwendet werden, dürfen keine Kontaminationsquelle sein. Es gibt daher verbindliche Vorschriften, die das Material und das Verfahren zur Herstellung der Komponenten berücksichtigen. Die wichtigste davon ist die Vorschrift, die in Italien als MOCA bekannt ist
Materialien und Gegenstände in Kontakt mit Lebensmitteln – LKM
Die Abkürzung LKM steht für Lebensmittelkontaktmaterialien (Materialien und Gegenstände, die mit Lebensmitteln in Berührung kommen). Es handelt sich um Materialien und Gegenstände, die dazu bestimmt sind, die Haltbarkeit von verpackten Lebensmitteln zu verlängern oder ihren Zustand zu erhalten und zu verbessern. Die Vorschrift schreibt vor, welche Materialien mit Lebensmitteln in Berührung kommen dürfen. Noch dazu gibt die Vorschrift die Verwendungs- und Herstellungsmethoden dieser Elemente an.
Insbesondere schreibt die Vorschrift vor, dass alle Materialien und Gegenstände nach guter Herstellungspraxis hergestellt werden müssen und unter normalen oder vorhersehbaren Verwendungsbedingungen keine Bestandteile auf Lebensmittel in Mengen übertragen dürfen, die
- eine Gefahr für die menschliche Gesundheit darstellen;
- eine unvertretbare Veränderung der Zusammensetzung der Lebensmittel herbeiführen
- eine Verschlechterung der organoleptischen Eigenschaften bewirken.
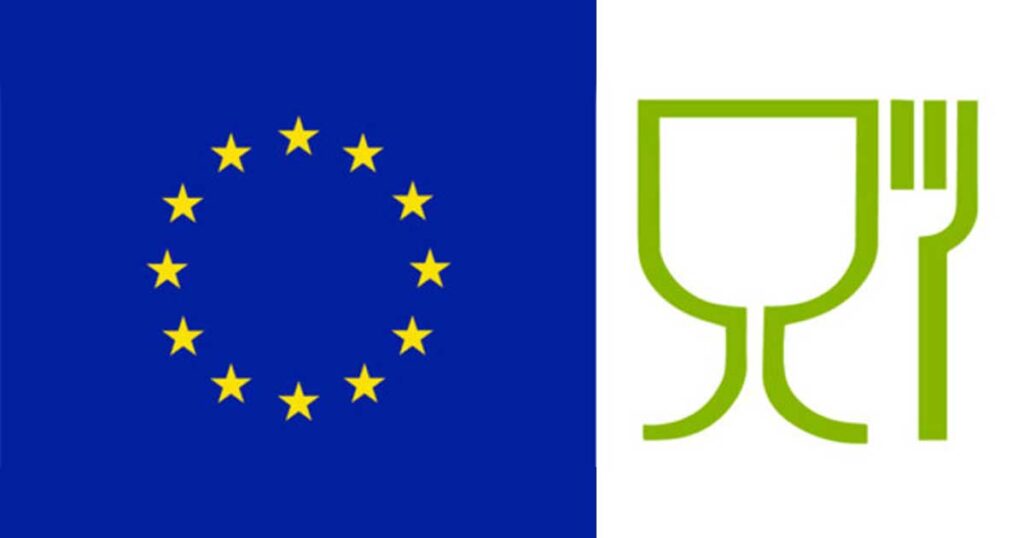
Produktionstechnik
Bei der Blechkaltumformung in der Lebensmittelindustrie werden hauptsächlich zwei Werkzeugarten gebaut:
FOLGEVERBUNDWERKZEUGE
Im Folgeverbundwerkzeug wird ein Blechstreifen bis hin zum fertigen Bauteil in mehreren Operationen umgeformt. Die Folgeverbundwerkzeuge eignen sich besonders bei Teilen, die in großen Stückzahlen beschnitten und gebogen werden. Bei kleineren Stückzahlen ist das Folgeverbundwerkzeug keine gute Lösung. Die Werkzeugkosten wären in der Tat zu hoch und würden jedes Teil erheblich belasten.
Der Einsatz von Folgeverbundwerkzeugen in der Lebensmittelindustrie ist besonders vorteilhaft: der Kontakt mit den Bauteilen wird minimiert und die Kontaminationsgefahr wird somit ausgeschlossen. Aus dem Coil wird der Blechstreifen abgewickelt und direkt in das auf der Presse eingebauten Werkzeug eingelegt. Das Beschneiden und das Biegen der Teile erfolgt automatisch, ohne dass die Komponenten selbst berührt werden müssen. Abgesehen von der Verwendung von Schmierölen während der Teilfertigung erhält man ein nicht kontaminiertes Bauteil. Es gibt spezielle Schmiermittel, die nach der Teilfertigung verdampfen und das Bauteil sauber hinterlassen.
Es ist wichtig, bei der Festlegung der Produkteigenschaften die Art des Schmiermittels zu überprüfen, das in der Presse verwendet werden kann. Solche Werkzeuge werden normalerweise in mechanischen Pressen eingebaut, die eine höhere Produktivität durch eine höhere Anzahl von Hüben pro Minute sicherstellen.
Kappen, Halterungen und kleine Behälter sind die typischen Anwendungen für solche Werkzeuge, unabhängig vom verwendeten Material.
ZIEHWERKZEUGE
Für die Herstellung von große, gebogenen Teilen oder von Lebensmittelbehältern, wie z. B. Stahl- oder Aluminiumschalen, werden am häufigsten Tiefziehwerkzeuge verwendet.
Diese Produktionstechnik ist komplexer, und insbesondere beim Tiefziehen vom rostfreien Stahl gibt es wichtige Einschränkungen, die berücksichtigt werden müssen, um Endprodukte innerhalb der Maßtoleranz, ohne Falten und andere Oberflächenfehler zu erhalten. Das Tiefziehen ist ein Verfahren, bei dem das Material während des Umformprozesses gezogen wird. Was scheinbar eine Einschränkung dieser Technik ist, ist in Wirklichkeit ein Vorteil beim Tiefziehen von Bauteilen für die Lebensmittelindustrie.
Das Kalttiefziehen vom Blech setzt nämlich voraus, dass das herzustellende Teil keine 90°-Winkel aufweist. Die Formen müssen weich sein und die Biegeradien müssen groß sein: Je höher das kaltgezogene Teil, desto größer müssen die Auslaufradien der Oberflächen sein. Bei der Herstellung von tiefgezogenen Teilen für Lebensmittel (z. B. Schalen und Behälter) wird diese Besonderheit zu einem wichtigen Punkt: diese Technik schließt Ecken aus, in denen sich Schmutz festsetzen kann.
Die abgerundete Teilform erleichtert die Reinigung. Ein kaltgezogenes Teil ist sehr günstiger als ein geschweißtes Teil und noch dazu auch viel einfacher zu reinigen .
WIE WIR WERT SCHAFFEN
Bei der Entwicklung von Produkten für die Lebensmittelindustrie sind wir in der Lage, die kundenspezifischen Anforderungen zu erfüllen.
SIMULATIONEN
Wir haben die Möglichkeit, Simulationen durchzuführen, damit wir den Prozess effektiv angehen können, indem wir ihn zum Zeitpunkt der Formgebung robust machen.
Dieser Schritt ermöglicht es uns, alle Änderungen am Bauteil noch vor der Werkzeugkonstruktion mit dem Kunden abzustimmen.
OPTISCHER SCANNER
F.lli Poli verfügt über einen optischen Scanner neuster Generation. Dieses Gerät ermöglicht es, die Richtigkeit der Abmessungen und der Formen von den hergestellten Bauteilen zu überprüfen, egal ob es sich um ein Folgeverbund- oder Tiefziehverfahren handelt. Die Abmessungen des Bauteils werden auf beiden Seiten erfasst und die Messergebnisse werden miteinander kombiniert: auf dieser Weise ist die Teildicke Punkt für Punkt überprüfbar, ohne das Teil zerschneiden zu müssen (d.h. mit einer zerstörungsfreien Prüfung).
Bei besonders wichtigen Sicherheitsanforderungen ermöglicht diese Messtechnik die Konsistenz der technischen Merkmale des Bauteils zu überprüfen.
DAS 3D-LASERSCHEINDEN
Das tiefgezogene Teil kann dann 3D-laserbeschnitten werden: das Beschneidwerkzeug ist somit überflüssig. Das ermöglicht eine erhebliche Kostenreduzierung. Das ist sehr wichtig für den Kunden: bei neuen Produkten sind die Verkaufsprognosen oft unsicher, insbesondere in der Anfangsphase.
Das Tiefziehen erfordert sowohl den Einsatz vom Ziehwerkzeug zur Teilformgebung als auch vom Beschneidwerkzeug zum Beschneiden des gezogenen Teils. Das Beschneidwerkzeug ist nicht günstiger als das Ziehwerkzeug (insbesondere bei großen Beschnittkonturen).
F.lli Poli verfügt über eine 3D-Laserschneideanlage und das ermöglicht dem Kunden deutliche Kostenvorteile. Dank der 3D-Laserschneidentechnik können wir auch sehr komplexe dreidimensionale Schneidpfade verfolgen und Ausschnitte sowie Beschneidkonturen am Bauteil fertigen. Der Kunde kann die Investition in das Beschneidwerkzeug aufschieben, bis das Produkt auf dem Markt erfolgreich ist.
PROTOTYPENBAU
Das 3D-Laserschneiden senkt nicht nur die Investitionskosten, sondern ermöglicht es uns auch, die ersten Prototypen in viel kürzerer Zeit herzustellen.
Für die Teilpositionierung auf der 3D-Laserschneideanlage müssen jedoch Schneidvorrichtungen angefertigt werden, deren Kosten und Vorlaufzeit jedoch wesentlich geringer als die des Beschneidwerkzeugs sind.
Einige Anwendungsbeispiele von F.lli Poli
Wir haben Erfahrung bei der Herstellung von Bauteilen für die Lebensmittelindustrie. Im Laufe der Jahre haben wir Anwendungen, insbesondere mit rostfreiem Stahl und Aluminium entwickelt. Hier unten finden Sie einige Anwendungsbeispiele
Ein Beispiel für Exzellenz
Wir arbeiten mit einem Start-up-Unternehmen zusammen, das ein sehr interessantes Produkt auf den Markt gebracht hat: Cicara®. Es handelt sich um ein Produkt, das die Art und Weise, wie Menschen ihren Kaffee trinken, revolutioniert. Hauptziel ist die Abfallreduzierung durch die Einsparung von Tausenden von Plastik- und Papierbecher.
Cicara® besteht zu 100 % aus recycelbaren Materialien.
Das Gehäuse und der Verschluss bestehen aus biologisch abbaubarem Biokunststoff, der aus erneuerbaren Quellen gewonnen ist und auf Maisstärke basiert.
Der Becher besteht aus rostfreiem Stahl AISI 316, der nach dem Tiefziehen entsprechend behandelt wird, um mit allen Speisen und Getränken kompatibel zu sein. Die Anwendung war technisch sehr anspruchsvoll.
Das Produkt wird mit einem Folgeverbundwerkzeug hergestellt, das von F.lli Poli konstruiert und gebaut wurde. Auch die Bauteilproduktion erfolgt beim Werk von F.lli Poli in Fara Vicentino.
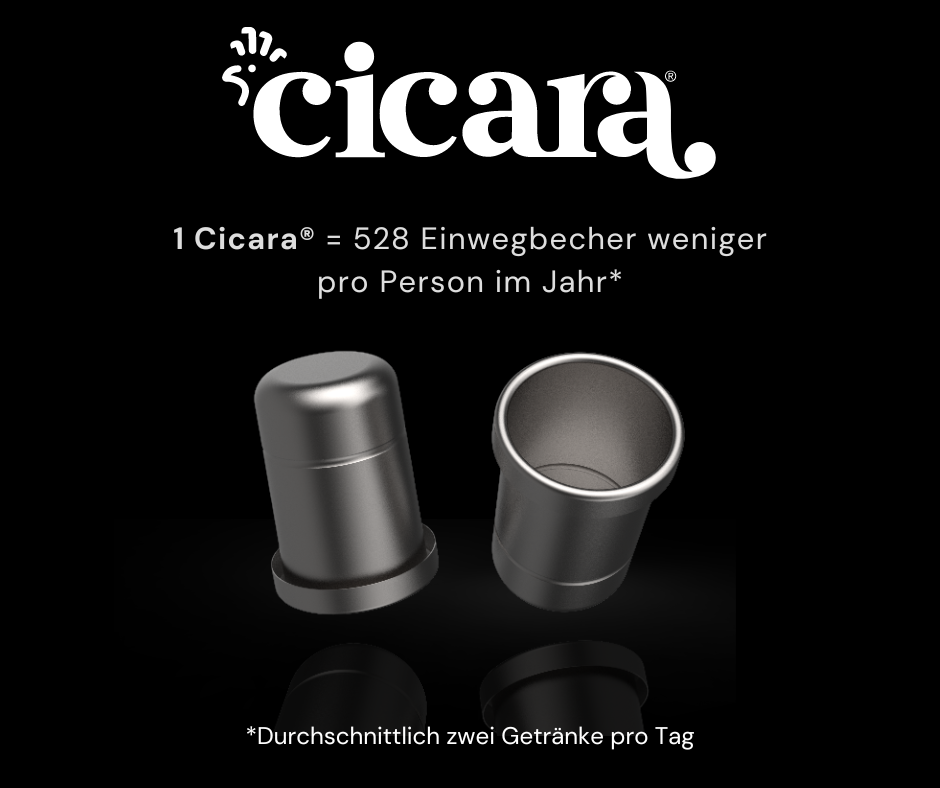
Das Werkzeug ist sehr komplex und besteht aus elf Operationen; der Ziehvorgang ist auf sechs Operationen unterteilt. Besonders herausfordernd war es, den Kragen am Becher zu bilden, der mit den Lippen des Benutzers in Kontakt kommt. Nach der Kundenvorgabe durfte der Becher keinen ästhetischen Fehler aufweisen. Aufgrund der Bauteilgeometrie war das Risiko, dass am Kragen Oberflächenfehler aus ziehvorgangbedingten Falten sichtbar waren. Daher wurde besondere Sorgfalt bei der Konstruktion dieses Werkzeugsteils angewandt. Es handelt sich um ein komplexes Werkzeug, das die Teilherstellung aus einem Metallstreifen ermöglicht.
Aus dieser komplexer Entwicklungsarbeit entstand das im Bild gezeigte Werkzeug.
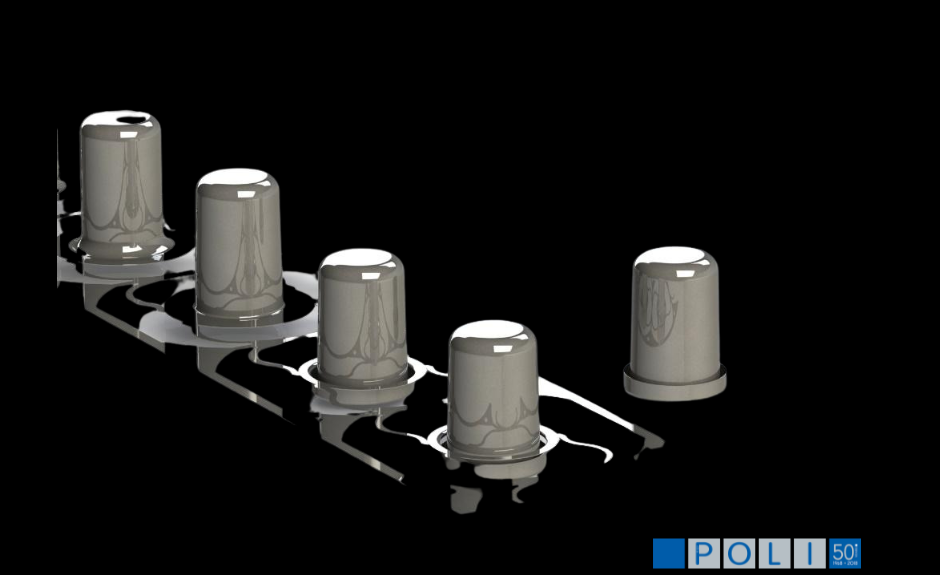
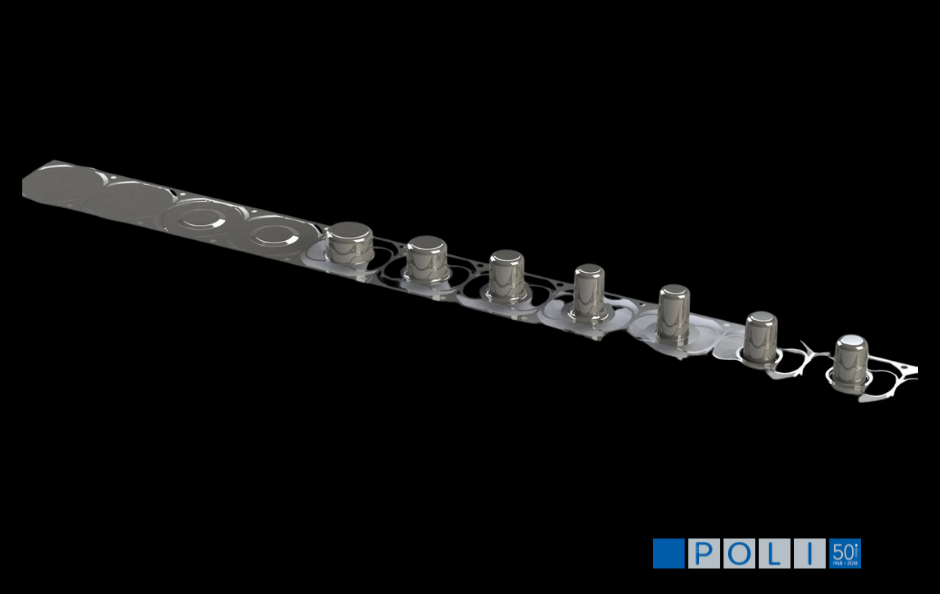
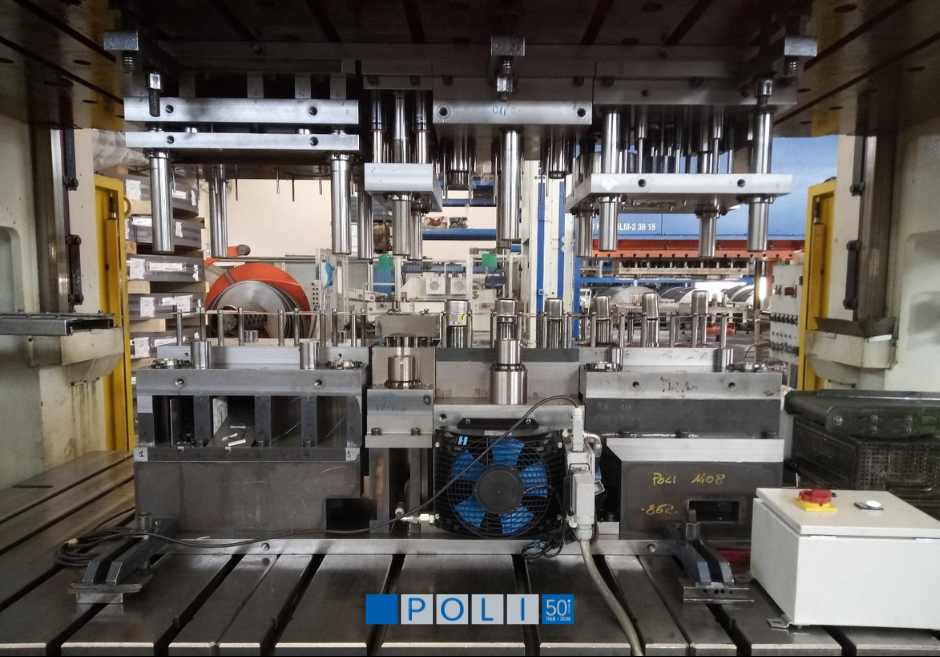
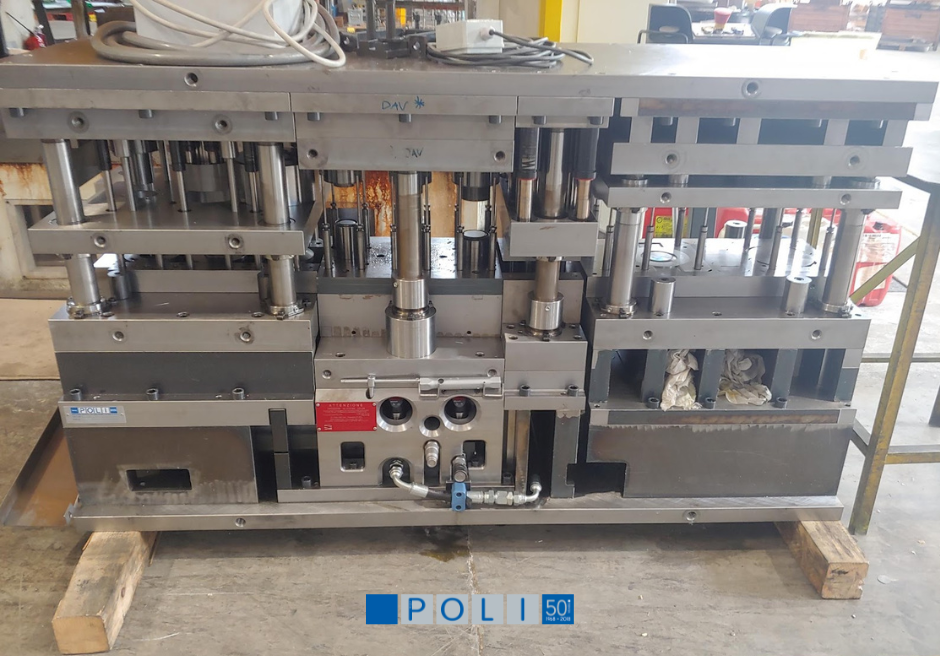